Sustainability
To help conserve local water resources and prevent pollution, we are investing in technologies and processes to save water and treat wastewater effectively. This includes water-saving manufacturing lines, dyeing material, and installing chemical recovery and water treatment units.
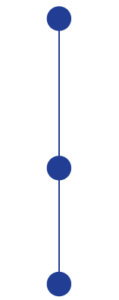
In Yarn Dyeing process, we have acheived a tremendous reduction in liquor ratio from 1:12 to 1:2.5 through process optimization techniques for reduction in water consumption
Liquor ratio in Space Dyeing process has dropped from 1:4 to 1:2
Most updated technology “Magic Rain Water, Less Yarn Dyeing” is adopted in Yarn Dyeing Department
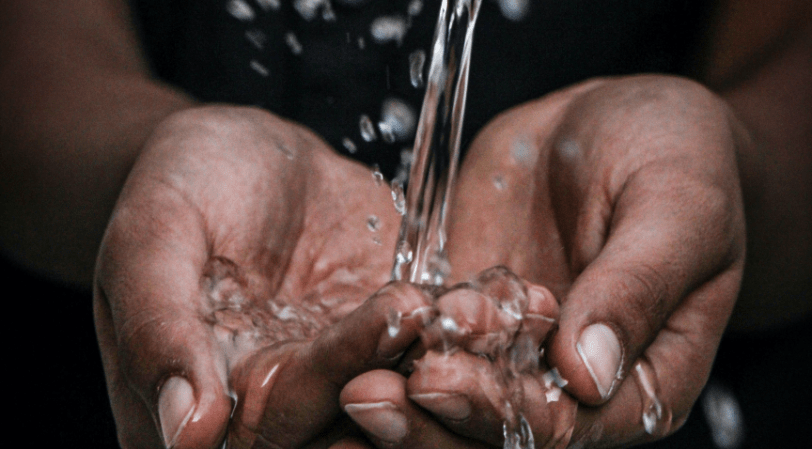
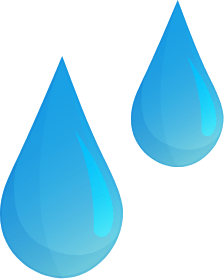
50%
Reduction of water consumption with use of pigment dyeing. Also reducing the process route of Tencel/Loyocell fiber for Dyeing program
50K
Cubic meters of water saved annually by replacing cooling tower with radiator for engine cooling
Effluent Treatment Project
The overall objective of the Effluent Treatment Project is to enable the textile wet processing effluent to comply with national and international environment legislation and standards and preserve water resources and ecological marine lives. It enables us to ensure that highest standards of quality and cleanliness are passed on to the community and environment. Our Effluent Treatment technology comprises physiochemical and biological treatment having total capacity of 5,000 m3/day, with 20% buffer capacity and backup of major equipment ; in emergency situations we have alternative equipment for operation. We have developmed in-house testing with most advanced equipment in order to monitor our effluent treatment scheme continuously. Effluent water analysis through an external laboratory is being carried out on a monthly basis. Our Sludge is being collected by Govt. licensed party for incineration.
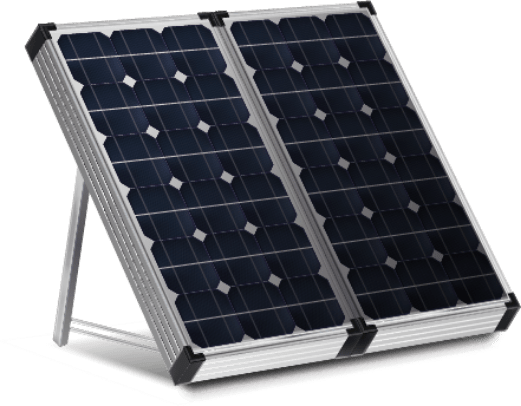
Installation of 5.2 MWh Solar PV System
Ibrahim Textile Industries marked its prolong commitment to sustainable development and renewable energy generation by investing in 5.2 MWh on grid connected rooftop solar photovoltaic system comprised of most updated bifacial technology. Ibrahim Textile Industries has initiated the biggest ever renewable energy project in the textile sector of our region and is by far the largest solar powered textile factory in Pakistan today.
Efficient Power Generation
Ibrahim Textile Industries has its own in-house production plant and therefore is not dependent on electricity supply.
20 MWh
Electricity generation capacity which is running on least polluted fossil fuel and most updated fuel efficient engines based on LINOX technology.
60%
Steam energy comes from waste heat recovery boilers using the heat from exhaust heat of engines as well as we have installed hot water and heat absoprtion chilllers 100% running on Jacket water from electric power engines.
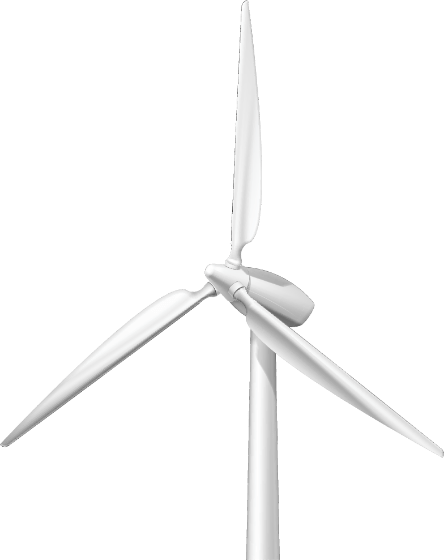
Energy Conversion
We have reduced energy consumption inside the mill by implementing a number of projects with the help of best available technology,equipment upgradation and process optimization.
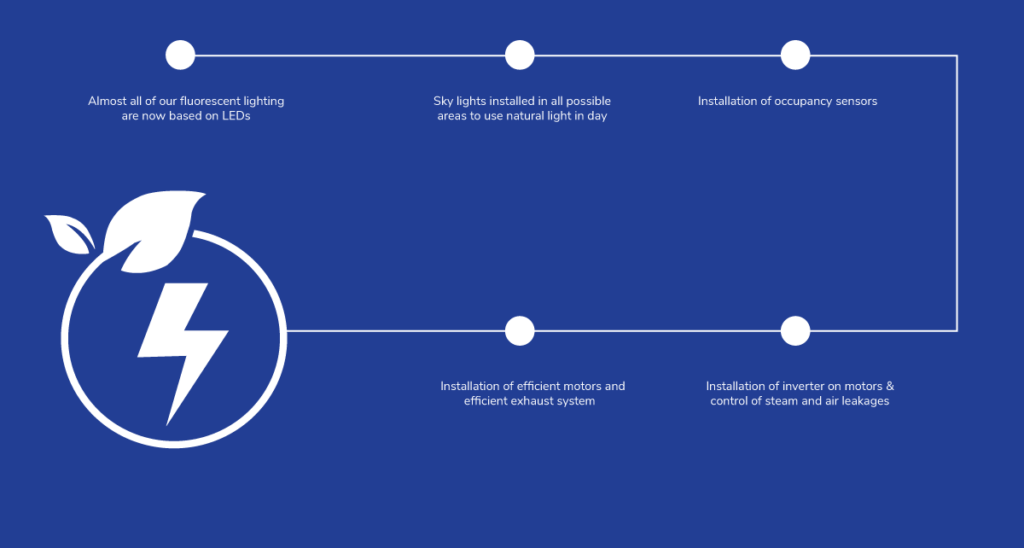




